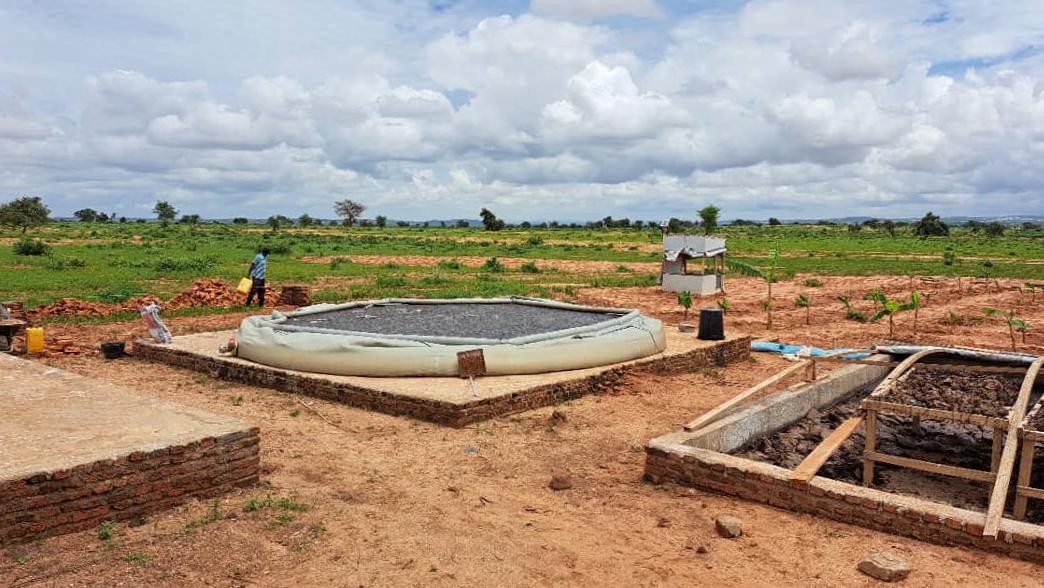
The "poop factory" of Aboutengue camp: A sustainable solution for community
In 1 click, help us spread this information :
Doctors Without Borders/Médecins Sans Frontières (MSF) constructed a faecal sludge treatment site in Aboutengue camp, eastern Chad, which hosts approximately 45,000 Sudanese refugees. This site processes waste from 932 latrines built by MSF, supporting improved sanitation and helping to meet the standard of 50 people per latrine in emergency contexts.
Locally referred to as the "poop factory," the pilot project is an innovative solution to treat and safely dispose of sludge from latrines, allowing for the use of dry sludge for farming and promoting environmental sustainability.
Charlotte Maupu, former MSF deputy water and sanitation coordinator in the camp, explains how the treatment site works and its impact.
What are the benefits of building a faecal sludge treatment site?
When latrines are full, we either close them permanently or desludge them. Desludging involves pumping out the waste, digging a hole, dumping the waste inside, adding lime, and sealing it off. However, this traditional method risks polluting the soil and groundwater, which can harm both the environment and people’s health.
To address this, we built this dedicated faecal sludge treatment site on the outskirts of the camp. The site is far enough from residential areas to avoid disturbing the camp. At the moment, the treatment site covers 3,600 square meters.
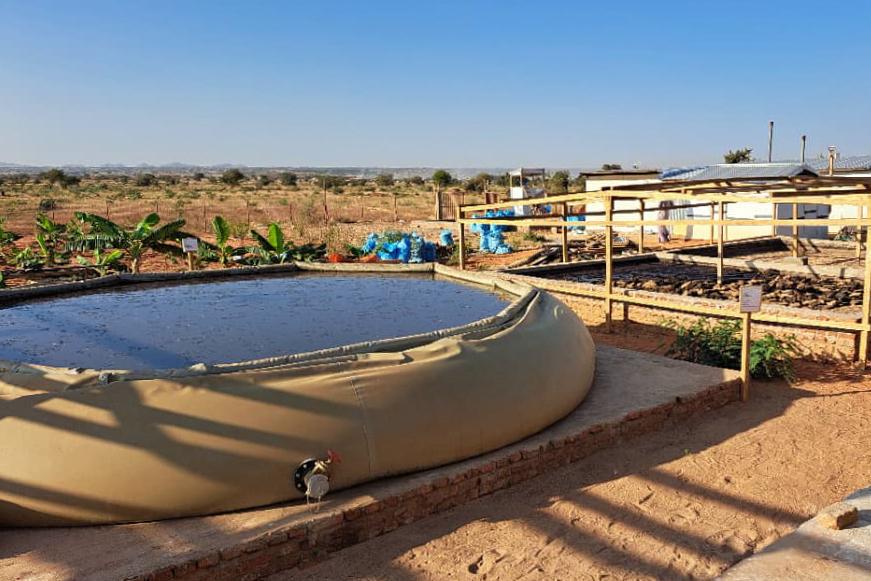
It’s important to clarify that this isn’t a traditional water purification station. Instead, our goal is to neutralize harmful bacteria and pathogens in the waste—a process known as "hygienization."
How does the treatment process work?
The process begins with pumping waste from the latrines. When trucks can’t access certain areas, especially where informal shelters are built, we use portable pumps. The waste is then transferred to a deposit tank, where we add lime—one part lime for every five parts waste. Using a pump system, we circulate and mix the lime with the waste, which raises the pH- a measure of how acidic or basic a substance is- to 12, making the environment too basic for most bacteria and pathogens to survive. We let this mixture sit for 48-72 hours.
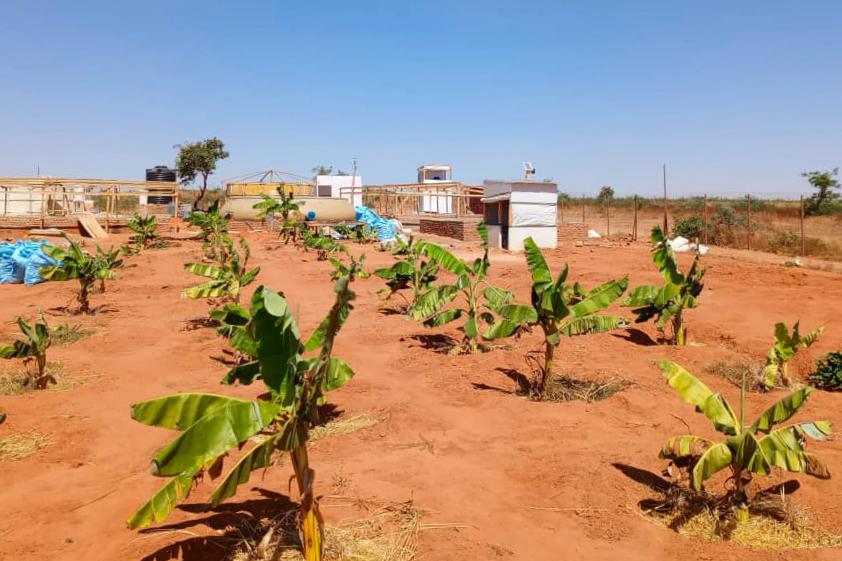
During this resting period, the waste separates into layers: water rises to the top, and denser sludge settles at the bottom. We then treat each layer separately.
For the water output, we drain it into another tank where it rests for several days until the pH returns to neutral. From there, it flows into infiltration trenches lined with gravel and stones to help it filter into the soil. To prevent waterlogging, we’ve planted banana trees around the site, which absorb up to 200 liters of water daily. These trees will soon produce bananas that are safe to eat.
For the sludge, we focus on drying it out through a two-step process. First, we spread the sludge on drying beds made of sand and gravel, which allow water to drain out by gravity. Once the sludge is semi-dry, we transfer it to a second concrete drying bed to remove any remaining moisture.
Lastly, we’re testing a third step: incineration. Burning the dried sludge ensures that any remaining pathogens, especially intestinal parasites (helminths), are destroyed. The incinerator is built over a pit, allowing us to easily dispose of the ash. Once the pit is full, we can either empty and bury the ash elsewhere or move the incinerator to a new location.
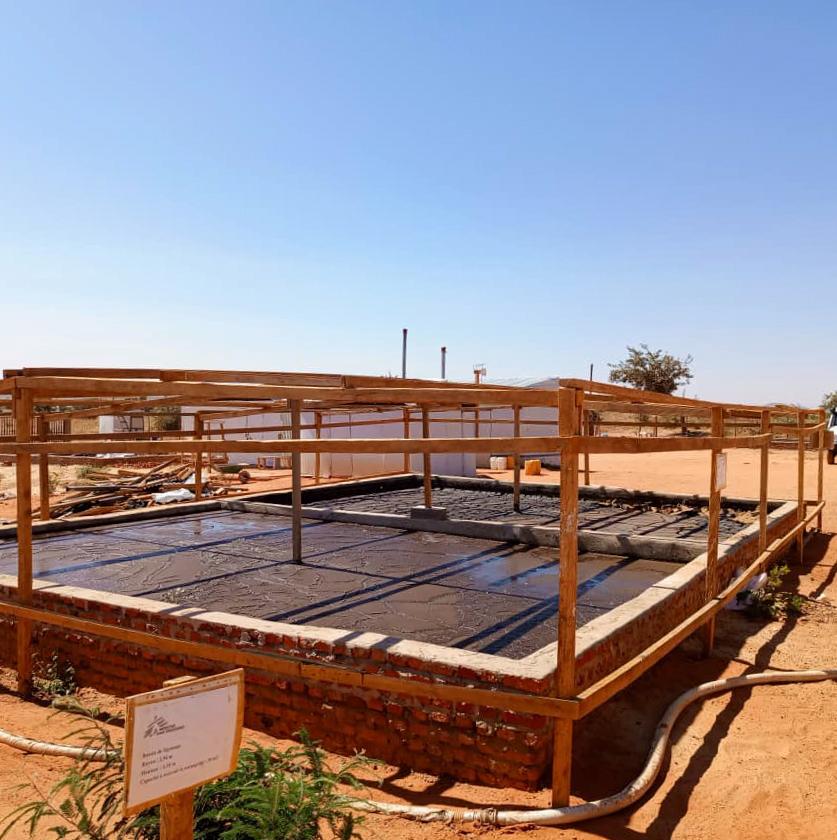
Can the output of this treated waste be reused ?
The dried human waste is rich in nitrates and phosphates, which are valuable nutrients for agriculture. In theory, it could be repurposed as fertilizer for local farmers. However, at this stage of our work, further analysis is required to confirm its safety before widespread use, and we currently lack the capacity to conduct those tests.
This is a new approach for MSF, what’s the best thing about it?
It’s the first time we’ve built such a treatment site in a non-epidemic context, and at this scale, it’s capable of handling waste for more than 45,000 people. The site operates with a team of 11 staff members, including four hygienists.
While other organizations have used similar methods before, this project has taught us many vital lessons. For example, we had to resize parts of the treatment site and rebuild the concrete drying beds to improve water flow.
This project stands out because it’s not only focused on sanitation but also on environmental sustainability.
It requires minimal energy to operate, apart from the fuel needed for the motor pumps. In the future, we may explore using solar-powered pumps to make the system even more eco-friendly.